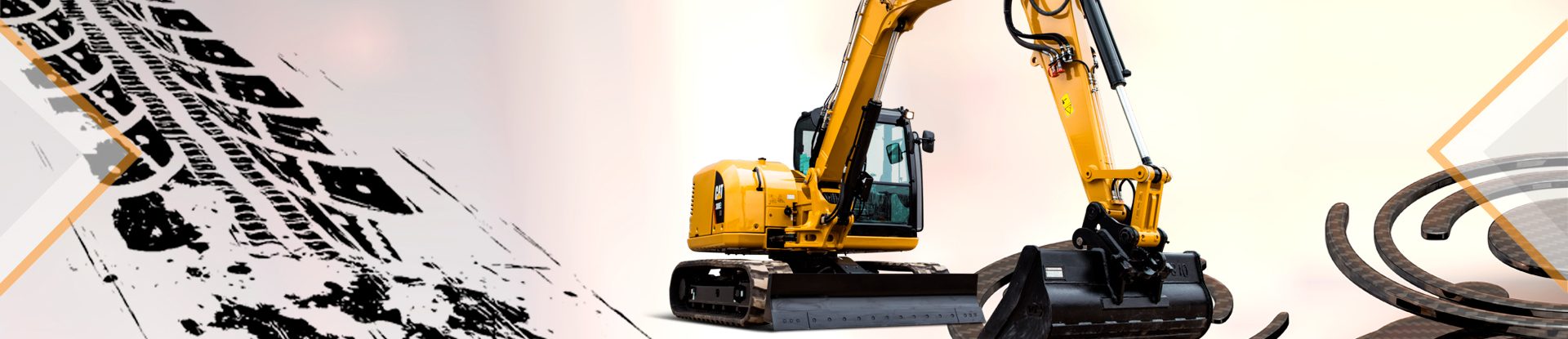
Disadvantages of rubber and metal tracks
The configurations of an undercarriage based on the material from the tracks is a determining factor when it comes to maximizing productivity or looking for specific results in a workspace.
The most popular option will be the use of rubber such as rubber and metal, which will have their series of negative aspects.
Metal track setup
1.-Cost: The first negative aspect of a metal track configuration will be its cost, which can range from 20 to 50% higher compared to its rubber counterpart. Also, the monetary value designated for the maintenance of metal track equipment is generally absorbed by the undercarriage components in values that oscillate 50%.
2.- Vehicle footprint: Vehicles whose movement is on metallic tracks leave significant marks on the surface on which they are working. If you want to minimize track damage on paved work areas or landscaping, the steel configuration is not the best option especially if the vehicle is medium to large.
3.-Noise: In urbanized environments in which is needed to comply with noise regulations during the execution of a work, metal tracks are at a disadvantage. The friction with the ground coupled with the not suitable properties of the material based on the absorption of shock and vibrations cause a high amount of noise compared to a rubber track configuration.
4.-Weight and speed: The additional weight that is a metal track configuration in conjunction with a higher traction capacity directly affects the vehicle’s travel speed by making it slower than its counterpart with rubber tracks. While in a different scenario this could be an advantage in some environments, it’s not when it comes to reaching higher speeds.
Rubber Track Configuration:
1.- Useful Lifetime: Rubber tracks are currently far from maintaining a lifetime similar to a steel configuration. The application of these can be negative in environments that involve surfaces plagued by demolition debris and uneven rocks as they are exposed to damage.
2.-Traction: If you want to maximize the traction of the vehicle, a configuration of rubber tracks will be the least indicated option. Rubber tends to deform during the operating process, generating uneven load points, which results in uneven load distribution. If your jobs involve surfaces that demand high traction as mud, ice, snow, and sand, reconsider the advantages that a steel track offers you.
3.-Repair and maintenance: The inherent properties of rubber make it malleable at high temperatures and prone to being brittle on surfaces such as ice. If either of the two scenarios results in damage due to breaks or tears in the material, a repair will be hard because, in contrast to steel tracks, a link can’t be easily replaced.
The choice of a track configuration for its material should be made after analyzing its positive and negative points depending on the properties of the surface on which you want to work.