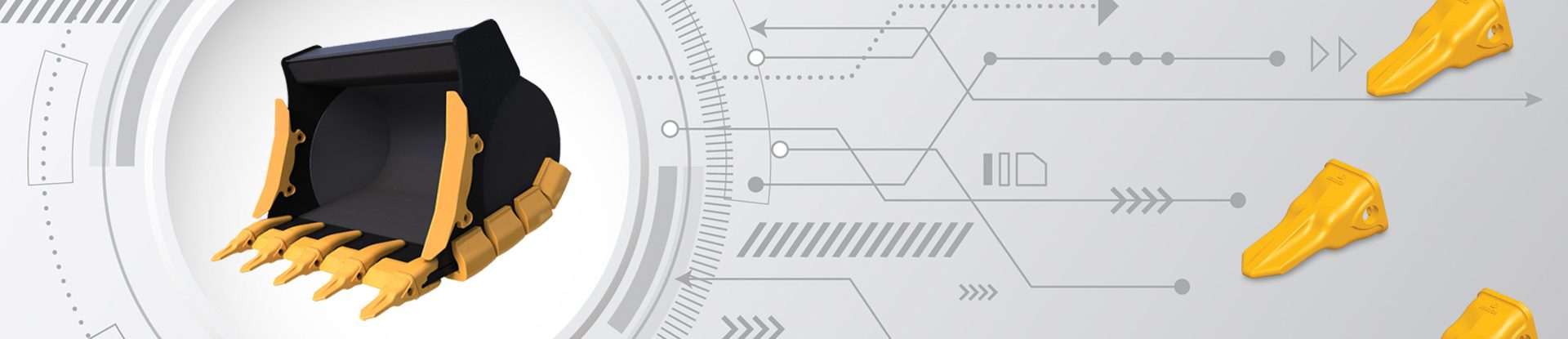
General Classification of Bucket Teeth on Heavy Machinery
The general condition of a service bucket teeth in excavation machines has a direct influence on the productivity of the equipment, if its integrity is optimal, it will minimize the mechanical stress transmitted to the machine, improves productivity triggering an extended useful life, and reducing maintenance costs.
Common mistakes made by owners of excavators, backhoes, and other earthmoving equipment is to use the same type of teeth for different tasks without considering the nature of the material they want to move or its properties. This limits machinery from reaching highly productive work rates, increases wear and tear, and minimizes the life of multiple components.
Before choosing the type of teeth your equipment will use, consider the following factors:
Teeth digging reach: The structural design of the teeth is associated with their digging reach. Analyze the type of soil, for example on compact, rocky, or frozen terrain, your best option will be sharp or pointed teeth because its smaller surface contact with the ground allows the service tool to efficiently moves through the material. On the other hand, teeth with relatively wide tips are used in not very compact surfaces or for handling materials.
Impact resistance: The teeth of a bucket have different designs according to the abrasive level of the work they will perform. To select the correct teeth, consider the nature of your soil.
Multiple machinery manufacturers offer their teeth classification system for which you should contact your parts supplier to know their properties and use, nevertheless, and, in many cases, in any brand, you can identify any of the following types:
Teeth Type: General purpose
This is the default configuration in an excavator bucket, its purpose is ideal for loosely packed or loose surfaces with low to intermediate abrasions with a medium-low impact level. Its use is foremost to trench digging.
For excavators in loose terrain with little abrasion and multiple applications. Specific for the realization of trenches and finishes. Impact: medium-low
Teeth type: Digging
Used in excavators that work on compact surfaces with high levels of abrasion and impact in which a high level of digging is required such as ice, rocks. Its shortcomings are the low useful lifetime.
Teeth Type: Double claw
They’re for highly compact surfaces with high impact levels, the digging level is higher compared to the previous example, it’s recommended to perform in low abrasive environments.
Tooth Type: Chisel
Widely used in excavators whose applications require medium-low penetration and impact, they have a high useful lifetime and the best digging range in the type of soil mentioned, despite, for abrasive materials they are not recommended.